Self Recuperative Burners

Self Recuperative Burners include a recuperator that is incorporated within the burner, which uses the heat of the flue gases to preheater the combustion air, This results in a reduction of fuel consumption and emission of Greenhouse gases by up to 30% depending on the process temperature and parameters. This Self Recuperative Burner is hydrogen ready and compatible, making it a suitable option for applications transitioning to clean hydrogen fuel.
We use a Silicon Carbide to make the heat exchanger increase the efficiency and life of the Heat Exchanger. The heat exchanger has a groove on its surface to increase the surface area to increase the efficiency of the heat exchanger.
These burners fire in Pulse firing Mode (ON/OFF Control)
They are ideal for heat treatment furnaces where we have a limited area available and where conventional Regenerative burners can not be used.
Key Benefits Of Self-Recuperative Burners
Enhanced Energy Efficiency
Self-recuperative burners are engineered to maximize energy recovery. By utilizing the heat from exhaust gases to preheat incoming air, these burners can achieve fuel savings of up to 30-50% compared to conventional burners.
Reduced Emissions
Lower fuel consumption directly correlates with reduced emissions. Self-recuperative burners help industries comply with stringent environmental regulations by significantly cutting CO2 and NOx emissions, contributing to a cleaner and healthier environment.
Cost Savings
The improved fuel efficiency of self-recuperative burners translates into substantial cost savings. Industries can benefit from lower energy bills, making these burners a cost-effective solution in the long run.
Operational Reliability
Designed for durability, self-recuperative burners require minimal maintenance and offer consistent performance over extended periods. This reliability ensures uninterrupted operations, enhancing productivity.
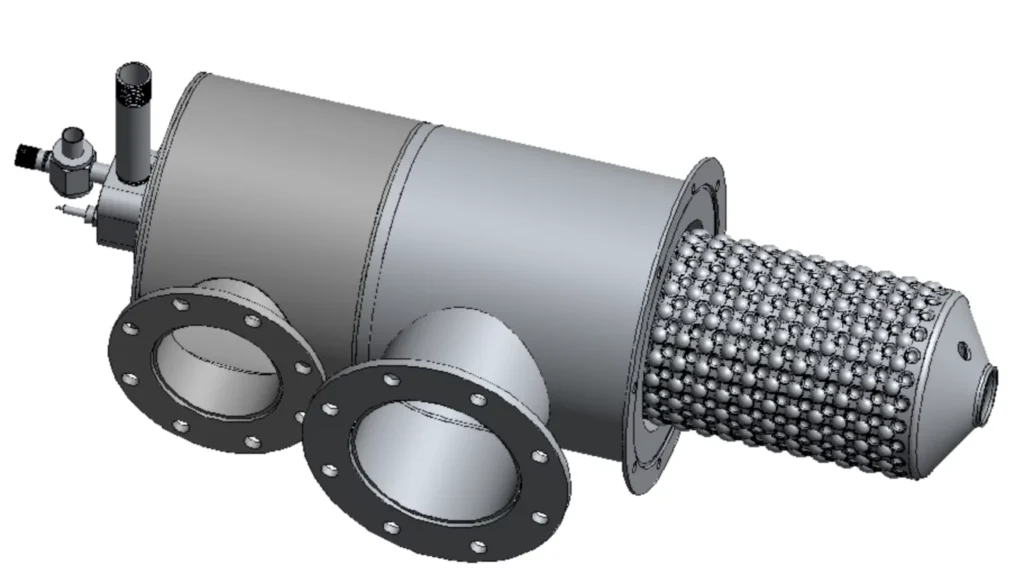

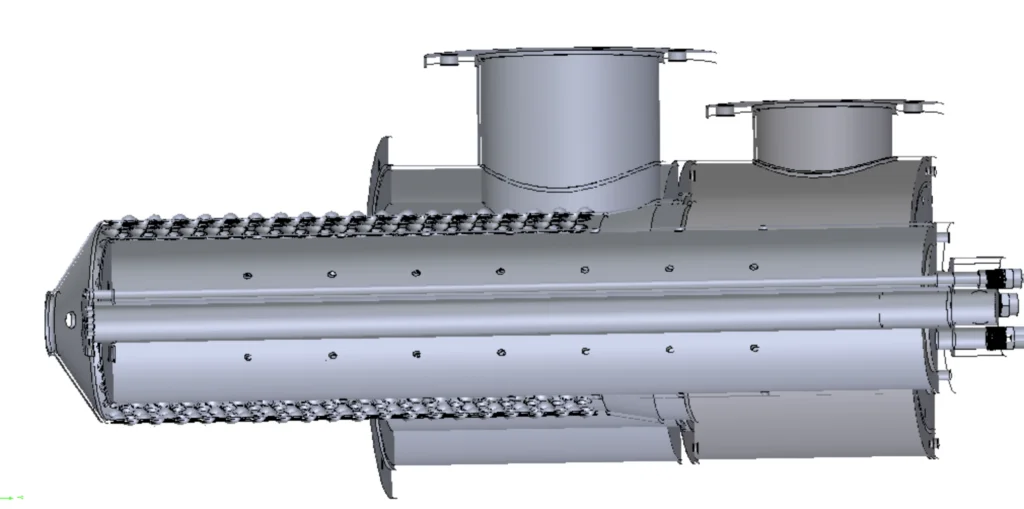
Working Of Self Recuperative Burner
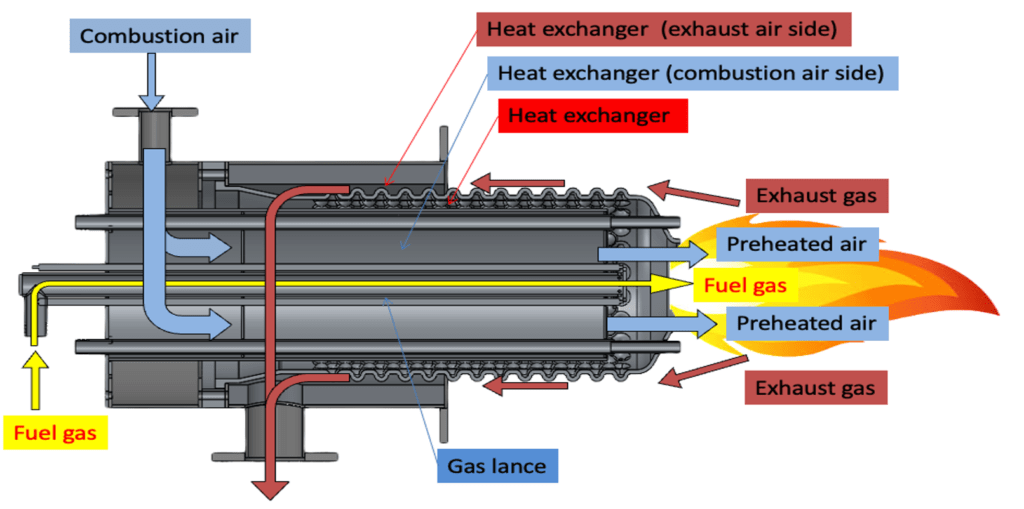
Why Choose Self Recuperative Burners by ENCON?
At ENCON, we are dedicated to delivering cutting-edge combustion solutions that meet the evolving needs of our clients. Our self-recuperative burners are designed with advanced technology to ensure maximum efficiency and sustainability.
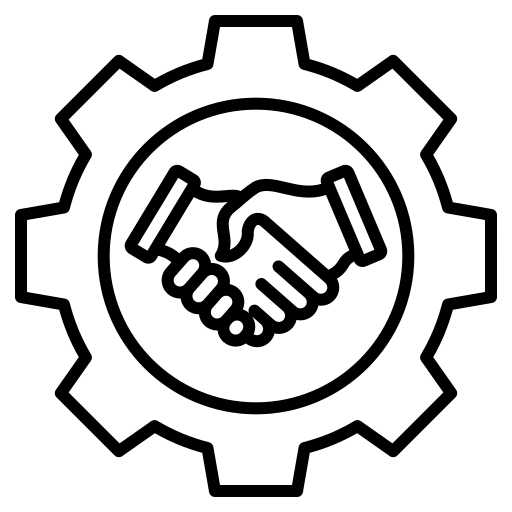
Expertise & Innovation
With years of experience in combustion technology, our team is committed to continuous innovation, providing solutions that are both effective and sustainable.

Custom Solutions
We understand that each industry has unique requirements. Our self-recuperative burners can be customized to meet specific operational needs, ensuring optimal performance.
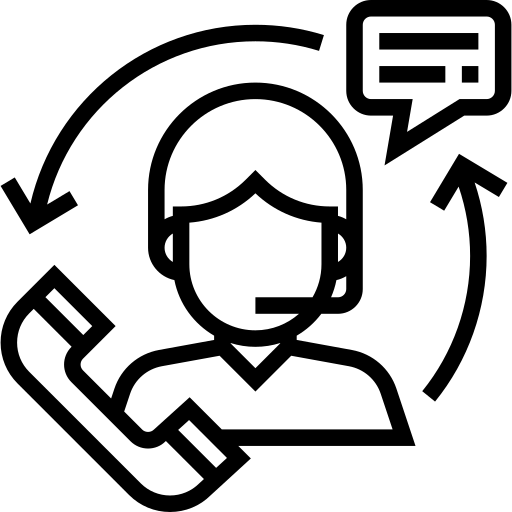
Comprehensive Support
From initial consultation to installation and maintenance, we offer comprehensive support to ensure seamless integration and operation of our burners.
Submit Your Requirements & Our Team Will Get Back To You Shortly!
Frequently Asked Questions
A self-recuperative burner is a type of industrial burner designed to improve energy efficiency by preheating the combustion air using the heat from the exhaust gases. This process, known as recuperation, reduces fuel consumption and enhances overall thermal efficiency.
Self-recuperative burners work by integrating a heat exchanger within the burner assembly. This heat exchanger captures heat from the hot exhaust gases and transfers it to the incoming combustion air. By preheating the air, the burner requires less fuel to achieve the desired combustion temperature, thus improving efficiency and reducing emissions.
The benefits of Using Self-Recuperative Burners are:
- Energy Efficiency: Significant reduction in fuel consumption due to preheated combustion air.
- Lower Emissions: Reduced carbon dioxide and nitrogen oxide emissions, contributing to environmental sustainability.
- Cost Savings: Lower fuel costs due to improved efficiency.
- Improved Process Control: Enhanced temperature control leading to more consistent product quality.
- Compact Design: Often designed to fit into existing systems with minimal modifications.
The lifespan of a self-recuperative burner can vary depending on the operating conditions, maintenance practices, and quality of the burner. Typically, these burners can last between 5 to 15 years.
These are the Maintenance Required for Self-Recuperative Burners are:
- Regular Inspections: Periodic checks for wear and tear, and ensuring all components are functioning correctly.
- Cleaning: Routine cleaning of the heat exchanger and burner components to prevent soot and residue build-up.
- Component Replacement: Timely replacement of worn-out parts such as seals, gaskets, and nozzles.
- Calibration: Ensuring proper calibration for optimal performance.
Self-recuperative burners are cost-effective in the long run due to their energy savings, reduced fuel costs, and lower emissions. The initial investment can be higher than conventional burners, but the payback period is typically short because of the significant operational savings.
Differences Between Self-Recuperative Burners and Conventional Burners are:
- Energy Efficiency: Self-recuperative burners use heat recovery to preheat combustion air, unlike conventional burners.
- Fuel Consumption: Lower in self-recuperative burners due to preheated air.
- Emissions: Reduced in self-recuperative burners.
- Complexity: Self-recuperative burners are more complex and require more maintenance.
Self-recuperative burners provide more consistent and controllable temperatures, which can enhance product quality by ensuring uniform heating and reducing defects caused by temperature fluctuations.
Installation Requirements for Self-Recuperative Burners
- Space: Adequate space for the burner and integrated heat exchanger.
- Insulation: Proper insulation to maximize heat recovery.
- Ventilation: Sufficient ventilation to manage exhaust gases.
- Compatibility: Ensuring compatibility with existing systems or making necessary modifications.
Safety Considerations for Using Self-Recuperative Burners are:
- Regular Maintenance: Ensuring all components are in good working condition to prevent malfunctions.
- Proper Installation: Correct installation to avoid leaks and ensure efficient operation.
- Monitoring: Continuous monitoring of burner performance and exhaust emissions.
- Training: Proper training for operators and maintenance personnel on the safe operation and maintenance of the burners
