Oxy Fuel Technology

Oxy Fuel Combustion Technology: A Path to Energy Efficiency and Sustainability
Oxy-fuel combustion technology represents a transformative approach to industrial heating, utilizing pure oxygen instead of air for combustion with fossil fuels (coal, oil, natural gas) and biomass. By excluding air from the combustion process, this technology achieves significantly higher flame temperatures, enhancing efficiency and reducing environmental impact.
Why Oxy-Fuel Combustion?

Increased Efficiency
- Oxy-fuel combustion reaches up to 3200°C, enhancing thermal efficiency with faster heating. These burners are hydrogen ready and compatible for sustainable, future-proof solutions.
- The higher flame temperatures lead to faster heating times and improved heat transfer rates and boosting thermal efficiency.
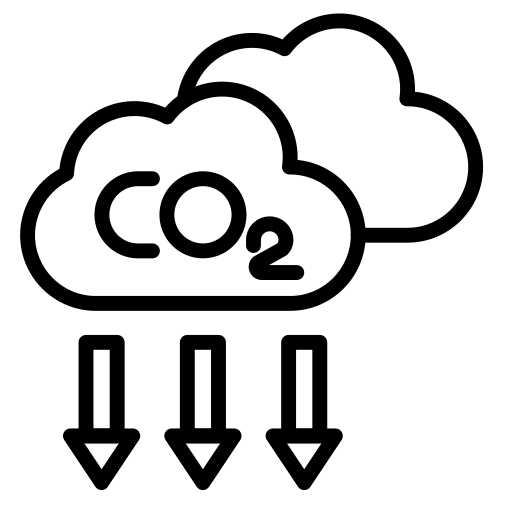
Reduced Emissions
- This technology drastically reduces CO2 and virtually eliminates NOx emissions due to the absence of nitrogen in the combustion process.
- It significantly lowers other greenhouse gas emissions, contributing to a healthier planet and helping industries comply with stringent environmental regulations.

Significant Fuel Savings
- Enhanced combustion efficiency results in substantial fuel consumption reductions. This can lead to significant cost savings and reduced environmental impact.
- Lower operational costs improve profitability while supporting sustainable practices. This makes them a win-win for businesses and the environment.
Sustainable and Cost-Effective Solutions
Industries such as steel, glass, and cement are leveraging oxy-fuel combustion to achieve remarkable gains in both operational efficiency and sustainability. At ENCON, we are dedicated to pioneering innovative solutions that drive energy efficiency and environmental sustainability.

Higher Flame Temperatures
Although flame temperatures can exceed 2,480°C and reach up to 3,200°C, process temperatures remain controlled, preventing damage to existing equipment and eliminating the need for new materials.

Environmental Impact
The exclusion of ambient air results in virtually no NOx emissions and a significant reduction in other harmful greenhouse gases, except for CO2.
Submit Your Requirements & Our Team Will Get Back To You Shortly!
Frequently Asked Questions
An oxy fuel burner is a type of industrial burner that uses pure oxygen (instead of air) mixed with a fuel source (such as natural gas, propane, or oil) to produce a high-temperature flame. This process enhances combustion efficiency and allows for higher flame temperatures compared to air-fuel combustion.
Benefits of Using Oxy Fuel Burners are:
- Higher Flame Temperatures: Achieve temperatures significantly higher than those possible with air-fuel burners.
- Increased Efficiency: More complete combustion of the fuel, leading to greater energy efficiency.
- Reduced Fuel Consumption: Lower fuel requirements due to the higher efficiency of oxygen combustion.
- Lower Emissions: Significant reduction in emissions, especially nitrogen oxides (NOx) and carbon dioxide (CO2).
- Improved Product Quality: Enhanced control over the combustion process, leading to more consistent heating and better-quality products.
Oxy fuel burners are commonly used in industries that require high-temperature processes, including:
- Ferrous & Non Ferrous : melting and heating
- Glass Manufacturing: Melting and shaping glass.
- Cement Production: Heating raw materials to produce clinker.
- Waste Treatment: Incinerating hazardous waste.
- Petrochemical Industry: Processes such as cracking and reforming.
Comparison to Traditional Burners
- Temperature: Oxy fuel burners can achieve higher temperatures.
- Efficiency: More efficient due to complete combustion.
- Fuel Consumption: Reduced fuel consumption compared to air-fuel burners.
- Emissions: Lower emissions, particularly NOx and CO2.
- Complexity: More complex and require pure oxygen supply.
Oxy fuel burners can use various types of fuel, including:
- Natural Gas
- Propane
- Butane
- Hydrogen
- Oil
Environmental Benefits of Oxy Fuel Burners are:
- Reduced Greenhouse Gas Emissions: Lower CO2 emissions due to higher combustion efficiency.
- Lower NOx Emissions: Significant reduction in NOx emissions because nitrogen from the air is not present in the combustion process.
- Reduced Fuel Consumption: Less fuel needed to achieve the same heat output, leading to fewer overall emissions.
Safety Considerations for Using Oxy Fuel Burners
- Oxygen Supply: Safe handling and storage of pure oxygen to prevent leaks and fire hazards.
- Flame Control: Proper flame control to prevent flashbacks and overheating.
- Ventilation: Adequate ventilation to handle exhaust gases and maintain a safe working environment.
- Training: Comprehensive training for operators on safe handling and emergency procedures.
The typical lifespan of an oxy fuel burner can range from 5 to 15 years, depending on usage, maintenance practices, and operating conditions.
Industries Benefiting the Most from Oxy Fuel Burners
- Metal Processing: Including steel mills and foundries.
- Glass Manufacturing: For melting and forming glass.
- Cement Production: For producing clinker.
- Waste Treatment: Especially hazardous waste incineration.
- Petrochemical Industry: For processes requiring high temperatures and efficient combustion.
Limitations of Using Oxy Fuel Burners
- Cost: Higher initial investment and operating costs due to the need for pure oxygen.
- Complexity: More complex system requiring specialized handling and maintenance.
- Safety: Increased safety risks due to handling and storage of pure oxygen.
- Infrastructure: Requires an oxygen supply infrastructure, which may not be available in all locations.
